Erros Comuns na Gestão de Fábricas e Como Evitá-los
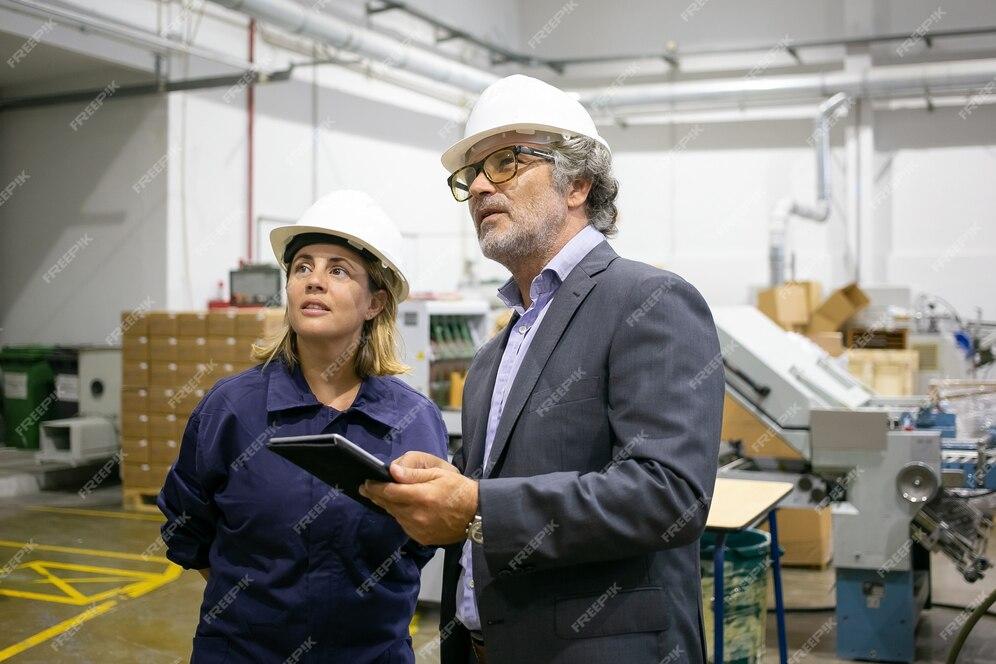
Foto: Divulgação
A gestão de fábricas é um processo complexo que envolve a coordenação de diversas atividades, desde a produção e controle de qualidade até a gestão de estoques e recursos humanos.
Erros nessa área podem ter consequências sérias, como atrasos na produção, aumento de custos e insatisfação dos clientes. Neste artigo, vamos explorar os erros mais comuns na gestão de fábricas e fornecer estratégias eficazes para evitá-los.
Falta de Planejamento
Um dos erros mais frequentes na gestão de fábricas é a falta de planejamento adequado. Muitas empresas iniciam a produção sem um planejamento sólido que considere a demanda, os recursos disponíveis e as capacidades da equipe. Essa abordagem pode levar a excessos de produção ou, inversamente, a falhas em atender às demandas.
Ao planejar a compra de itens específicos como calha para telhado preço, é importante alinhar as necessidades do mercado com os recursos disponíveis para evitar excesso de estoque ou falta de produtos essenciais durante a produção.
Ou seja, crucial que os gestores invistam tempo na elaboração de um plano estratégico de produção. Isso inclui a previsão de demanda, análise de capacidade e planejamento de recursos.
Utilizar softwares de gestão que forneçam dados em tempo real pode ser uma excelente maneira de ajustar o planejamento e garantir que todas as áreas da fábrica estejam alinhadas com os objetivos da produção.
Comunicação Ineficiente
Outra armadilha que pode comprometer a gestão de fábricas é a comunicação ineficiente. Em muitas organizações, a comunicação entre setores é fragmentada, o que resulta em mal-entendidos e retrabalho.
Informações críticas sobre prazos, mudanças de processo ou problemas em linha de produção podem não ser transmitidas, afetando a operação geral da fábrica. Uma comunicação clara e eficiente é essencial para a produção de itens específicos, como saco plástico para salgados congelados.
Quando os setores estão alinhados, é possível reduzir desperdícios de materiais, otimizar os processos produtivos e garantir um atendimento rápido e satisfatório aos clientes, fortalecendo a confiança na marca.
Logo, é essencial criar canais de comunicação claros e abertos. Reuniões regulares entre equipes de produção, vendas e logística podem ajudar a garantir que todos estejam na mesma página. Ferramentas de comunicação digital, como plataformas de gerenciamento de projetos, podem facilitar a troca de informações e o gerenciamento de tarefas.
Negligenciar a Capacitação da Equipe
O sucesso da gestão de fábricas está diretamente relacionado à capacitação da equipe. A negligência em treinar e atualizar constantemente os colaboradores pode resultar em uma equipe desmotivada e menos produtiva. Funcionários mal treinados podem cometer erros que impactam diretamente os resultados e a eficiência do processo produtivo.
Por exemplo, colaboradores bem treinados são capazes de manusear itens como porta etiquetas para gôndolas com facilidade, garantindo uma organização eficiente do estoque e agilidade na reposição de produtos. Essa capacitação contribui para um fluxo de trabalho otimizado e um ambiente mais produtivo.
Portanto, as empresas devem implementar programas de treinamento contínuo e desenvolvimento profissional. Oferecer capacitação em novas tecnologias e metodologias de produção não só eleva os níveis de eficiência, como também aumenta a satisfação dos funcionários.
Ignorar a Importância da Manutenção Preventiva
A manutenção dos equipamentos é um aspecto que muitas vezes é subestimado na gestão de fábricas. Ignorar as manutenções preventivas pode levar a quebras inesperadas, resultando em paradas de produção e custos elevados com reparos.
Para mais, a falta de manutenção pode afetar a qualidade do produto final, implicando em perda de credibilidade junto aos clientes. Equipamentos como martelo demolidor e rompedor, quando submetidos a inspeções regulares, garantem eficiência e segurança em sua operação.
Essa prática preventiva assegura a continuidade das tarefas essenciais, minimizando interrupções e mantendo o desempenho ideal em todas as etapas do trabalho. Logo, é crucial adotar uma rotina de manutenção preventiva.
Realizar inspeções regulares nos maquinários e criar um cronograma de manutenção pode assegurar que as máquinas estejam sempre em condições ideais de funcionamento. Essa prática não apenas minimiza interrupções na produção, mas também prolonga a vida útil dos equipamentos, resultando em economia a longo prazo.
Falta de Padronização de Processos
A padronização de processos é fundamental para garantir a qualidade e a eficiência na produção. Contudo, muitas fábricas falham em estabelecer normas claras e uniformes, o que leva a variações indesejadas na produção.
A falta de padronização pode resultar em produtos de qualidade inconsistente, além de dificultar a identificação de falhas nos processos. Imagine uma fábrica que produz itens personalizados e padroniza seus métodos para calcular o preço de trocador de calor.
Com essa abordagem, a empresa garante consistência nos orçamentos, proporcionando maior transparência e confiabilidade aos clientes. Essa uniformidade contribui para a satisfação do cliente, reforçando a confiança na marca e otimizando os processos internos.
Para evitar a falta de padronização, é importante documentar todos os processos e criar um manual operacional que sirva como guia para os colaboradores. Metodologias como Lean Manufacturing e Six Sigma ajudam a eliminar desperdícios e garantir eficiência na produção.
Conclusão
A gestão de fábricas é repleta de desafios, mas compreender e evitar erros comuns pode ser a chave para o sucesso. Planejamento, comunicação, capacitação, manutenção preventiva, padronização, controle de estoque e inovação são essenciais para uma gestão eficaz.
Ao abordar esses aspectos de forma proativa, as fábricas podem otimizar suas operações, aumentar a satisfação do cliente e, consequentemente, alcançar melhores resultados financeiros.